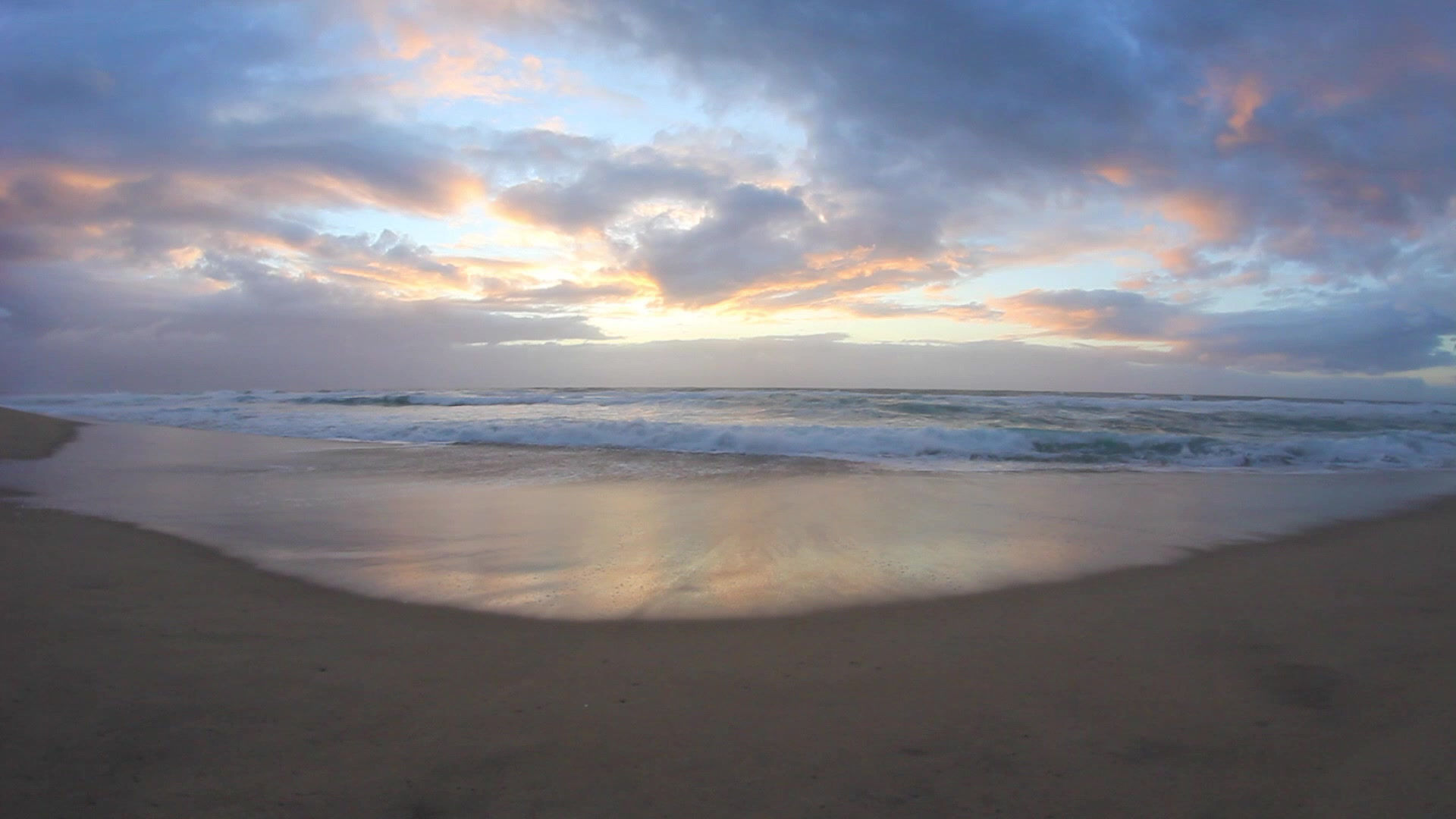
Creating Visual Aids to Yield Consistent Coding of Nonconformance Reports:
The most valuable and my favorite project was one where I assisted in a Corrective and Preventative Action (CAPA) response to an FDA 483 finding. This type of finding requires an immediate change to something within the company, which will allow the company to become more standard with FDA regulations. My role included developing 14 process-specific visual aids that would integrate the campus defect codes. NCRs are filed when an operator is machining, cleaning, or handling a part that has acquired a defect. When they file an NCR, a "code" has to be chosen which will be used to categorize the type of defect to the part. The goal was to yield consistent defect coding of Nonconformance Reports (NCRs) by updating the nonconformance product reporting procedure.
​
The Process:
To begin this project, I had conversations with the Quality and Manufacturing Engineers of all value streams on the campus to learn about the processes their shop floor team members follow while manufacturing parts. Along with hearing it from the Engineers, we also trended the NCRs based off of defect code and the description that was filled out with it. We were able to determine which defects were being commonly coded wrong.
​
The visual aid (linked below) is for all of the Metals Machining and In-Process Inspection works centers. We aimed to emphasize the common defects / nonconformances at the top of the visual aid, as that is what the user sees first. Along with that, there are leading questions to guide them to the correct defect code when reporting a nonconformance they have spotted. There are also pictures of common defects the team members would see at their work station, as well as colors, bolded words, and notes to touch on important details. The document highlights my ability to display large amounts of information in a non-technical, easy-to-follow way, which is an important skill to have when presenting projects to clients/audiences who are both technically and non-technically versed.
​
​
​
​
​
​
​
​
​
​
​
​
​
​
​
​
​
​
​
​
​
​
​
The Goal:
Our goal was to decrease the number of NCRs with an incorrect defect code. My colleagues and I were able to identify many of the root causes for all possible nonconformances, and were able to create defect codes to encompass these nonconformances. By using FDA regulations, 6 months of campus-wide NCR data, and root causes of all nonconformances we were able to justify the information covered in the visual aids. Particularly, I wrote 14 technical memos to justify the difference between common cause defects and special cause defects within each work center. Work centers are stations that operators work at when manufacturing parts. Once we revised the set of possible defect codes, we were able to create process-specific visual aids to hang at all work centers throughout the shop floor.
​
​
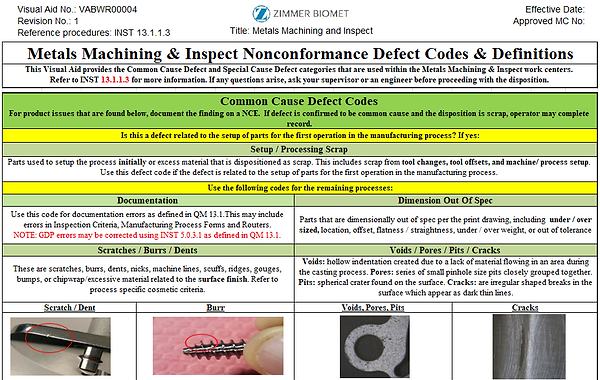